Yokogawa and DOCOMO Successfully Conduct Test of Remote Control Technology Using 5G, Cloud, and AI
Targeting remote, autonomous operations for the process industries
Yokogawa Electric Corporation announced that they have conducted a proof-of-concept test (PoC) of a remote control technology for industrial processing. The PoC test involved the use of an autonomous control AI, the Factorial Kernel Dynamic Policy Programming (FKDPP) algorithm*1 developed by Yokogawa and the Nara Institute of Science and Technology, in a cloud environment and a fifth-generation (5G) mobile communications network provided by DOCOMO. The test, which successfully controlled a simulated plant processing operation, demonstrated that 5G is suitable for the remote control of actual plant processes.
Latest Aithority Insights: Top Skills Needed to Become an AI Engineer
The trend to locate production facilities in remote and/or hazardous areas in recent years is fueling a growing demand for remote industrial operations and transforming how people work. Meanwhile, equipment used in plants to purify and refine resources and materials for essential products can deteriorate after many years of use, so remote, autonomous regulation and control would be hugely beneficial. One possible solution is to install edge devices equipped for high-speed wireless communications at plants and employ cloud-based autonomous control AI to control the equipment dynamically. Yokogawa has already proven that its FKDPP algorithm is a feasible autonomous control AI solution. In a field test at a chemical plant*2 this past February, for 35 days FKDPP successfully controlled processes known to be difficult to automate using existing PID*3 and APC*4 control technologies, and which therefore had been performed manually. The combination of FKDPP and the cloud with 5G, which offers low latency and the capability to connect a large number of devices, promises to be a core technology for achieving industrial autonomy.
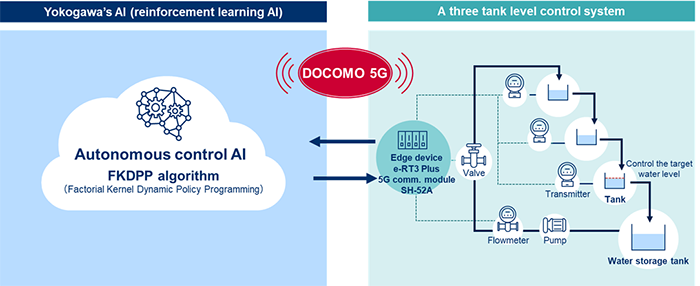
Following an agreement between Yokogawa and DOCOMO announced on April 14, 2021, the demonstration test was conducted to verify whether a three tank level control system*5 could be controlled using FKDPP in the cloud via a 5G network. A target water level was set, tests with low- to high-speed control cycles were conducted, and the effects of mobile-communications latency on FKDPP control were confirmed. Compared to 4G, the test demonstrated that especially with high-speed control, 5G delivers 1) lower latency, 2) less overshoot relative to the target water level, and 3) is capable of handling a control cycle as short as 0.2 seconds, thereby achieving better control for more stable quality and higher energy efficiency.
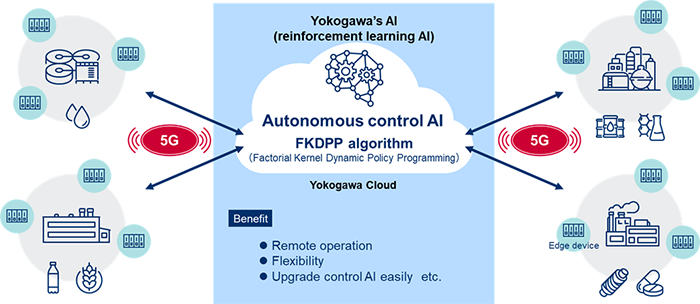
Yokogawa, which has been advocating the concept of industrial automation to industrial autonomy (IA2IA) since 2019, aims to apply 5G technology for remote plant control. In collaboration with DOCOMO and customers, it will continue carrying out advanced initiatives aimed at facilitating a shift toward industrial autonomy.
DOCOMO is continuing to enhance and evolve its network technologies, create advanced networks tailored to the needs of specific customers, and develop 5G solutions for diverse public and private purposes.
Top Machine Learning Insights: LivePerson Collaborates with UCSC to Build the Future of Natural…
Both Yokogawa and DOCOMO, as members of the 5G Alliance for Connected Industries and Automation (5G-ACIA), which is pursuing industrial applications for 5G, will continue to evaluate the use of 5G for remote, autonomous plant operations. By carrying out demonstrations in a wide range of customers’ plants and examining communications reliability and latency-related issues during long-term use, the companies will strive to achieve 5G and AI-enabled autonomous control. The 5G-ACIA will present the results of this demonstration test at Hannover Messe 2022*6, between May 30 and June 2.
-
The FKDPP AI algorithm, which uses reinforcement learning technology, can be applied to all kinds of control applications, including those that cannot be automated with existing control methods such as PID control or APC, to achieve conventionally challenging simultaneous goals, such as high quality and energy efficiency
-
See press release (In a World First, Yokogawa and JSR Use AI to Autonomously Control a Chemical Plant for 35 Consecutive Days:
-
Proportional-Integral-Derivative control, first proposed by Nicolas Minorsky in 1922, is an infrastructure-control technology for processing industries that is used to control items such as quantity, temperature, level, pressure, and ingredients. It implements control aimed at target values based on P, I and D calculations according to deviations between current and set values. In some cases, due to the characteristics of the mathematical expression, a value might exceed (overshoot) the set value or take time to settle to avoid overshoot.
-
Advanced Process Control uses a mathematical model to predict process responses and supply set values to the PID control loop in real time in order to improve productivity, quality, and controllability. It is easily applied for control to increase production, reduce labor time, and save energy. APC results in smaller deviations in data, making it possible to more closely approach the limits of operating performance (i.e., optimal performance), but it is not adept at responding to the rapid vaporization of fluids, similar chemical reactions, major changes in material composition, and changes in machinery.
-
A three tank level control system that is used for training and experiments involving the regulation of water flow from one level to the next with the aim of controlling the water level at the lowest tank.
-
One of the world’s largest international manufacturing exhibitions, which attracted some 6,500 companies and 220,000 people in 2019.
Read More About Aithority News : Fraud Mitigation Receives a Boost with SEON’s ML-based Blackbox Update
[To share your insights with us, please write to sghosh@martechseries.com]
Comments are closed.