NASA to Help Fund Analyswift, Purdue Technology Shown to Speed Design of Composite Deployable Structures
An innovation that helps speed the design of fishing rods, skis and cell phone electronics soon will help NASA do its work in space.
AnalySwift LLC, a Purdue University-affiliated commercial software provider, has received a $125,000 Small Business Technology Transfer (STTR) grant from NASA. The STTR award will help the company further develop its SwiftComp software, technology that provides efficient, high-fidelity modeling of deployable structures made of high-strain composites.
“This is an outstanding recognition and validation of our technology,” said Allan Wood, president and CEO of AnalySwift. “NASA is going to be able to use the software as it designs devices and structures to help achieve success in space exploration, including deployable structures and living vessels used in a space environment.”
Recommended AI News: Change Healthcare Unveils API & Services Connection, a Marketplace to Accelerate Innovation in Healthcare
Wood said the software would help NASA engineers model high-strain composites with a tradeoff between efficiency and accuracy that were unreachable using more conventional methods.
A composite is a material made from two or more different materials that when combined are stronger, lighter or have other advantages over those individual materials by themselves. A high-strain composite experience strains much higher than most other uses of composites.
Wood said NASA is looking to use the software technology, in part, to study deployables made of high-strain composites that are lightweight and feature time- and temperature-dependent behavior.
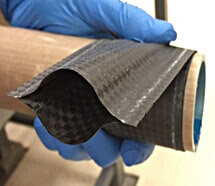
Recommended AI News: Seizing Artificial Intelligence’s Opportunities In The 2020s
In addition to deployable composite booms, NASA could leverage the software for structures such as living vessels, foldable panels, hinges and reflectors, as well as lightweight structures such as satellite buses, landers, rovers, solar arrays and antennas. Other applications include highly flexible wings for future aircraft and highly fatigue- and damage-tolerant structures for revolutionary vertical lift aircraft.
The technology was developed by Wenbin Yu, a professor of aeronautics and astronautics in Purdue’s College of Engineering.
“The unique synergistic relationship between Yu’s computational mechanics research group at Purdue and AnalySwift, with its SwiftComp simulation software, makes it a very efficient transition mechanism of new material and structures fundamental theory developments into the commercial world,” said Juan Fernandez, a research aerospace engineer with NASA. “The ultimate goal is to increase the capabilities of this commercial computational tool so that others in the high-strain composites community can benefit from it and help advance the field, while using it to satisfy current and future NASA program modeling needs.”
The software also has been licensed to companies and universities worldwide, including those using it for work on satellites and mobile phone components, including printed circuit boards.
“The software reduces analysis time from hours to minutes,” Wood said. “SwiftComp takes details of the fundamental building block of materials and structures as input, then outputs the structural properties needed for macroscopic analysis. It can be used for composite beams, plates and shells, and 3D structures, for both micromechanical and structural modeling.”
Recommended AI News: Host Analytics Rebrands as Planful
Comments are closed.